Quality Built® Tech Alert
September 4th, 2014
Volume 2, Issue 6
Seam Seal Tape
Every year we inspect thousands of homes with one brand or another of house wrap installed as the weather-resistive barrier. As energy costs increase and energy code requirements become more stringent, we are seeing house wrap installations where the seams are sealed.
Many house wrap manufacturers have proprietary seam seal tapes that they sell for exclusive use with their house wrap system. As implied by the name, the tape is used for sealing the seams of the house wrap. The purpose of sealing the seams is to create a continuous air barrier. Some of the manufacturers imply that the use of their tape will also reduce moisture intrusion.
The installation procedure for house wrap, regardless of the manufacturer, is fairly standard across the board. Installation begins with a course at the base of the wall and that course is overlapped horizontally with the next course. The amount of the horizontal overlap varies by manufacturer. Additionally, vertical seams must also be overlapped. Many of the problems related to the seam seal tape start with the wrap installation, particularly the fastener placement.
If the seams are going to be taped this generally occurs after the entire house is wrapped or after several courses of wrap are installed. Since most areas of house wrap are over wood-based sheathing, leaks at the seams may go undiscovered for years.
The horizontal seam tape is installed lapping over both layers of wrap. This means that the seam tape installation creates a reverse lap at the top of the tape. While this reverse lap might not result in leakage in laboratory conditions, in the field the installation of the tape is not always done properly. At times the wrap is not clean when the tape is applied. Other times the surface is damp preventing the tape from adhering properly. Oftentimes cap fasteners installed at the tape edge prevent a complete seal. Wrinkles in the wrap can leave voids at the tape contact surface. All of these conditions can allow water to migrate behind the tape, follow the horizontal seam to the nearest vertical seam, and ultimately into the structure.
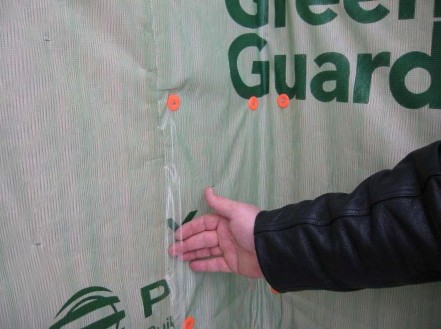
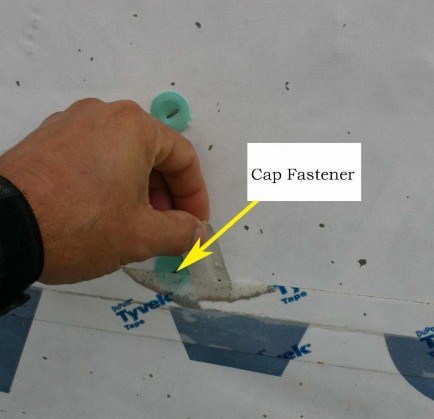
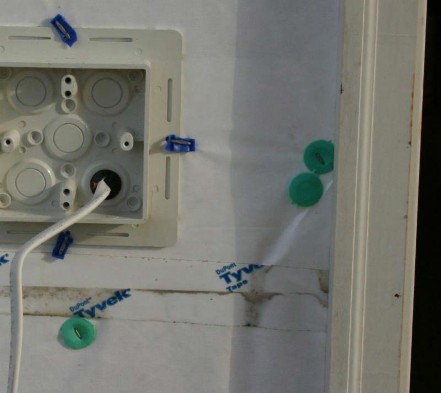
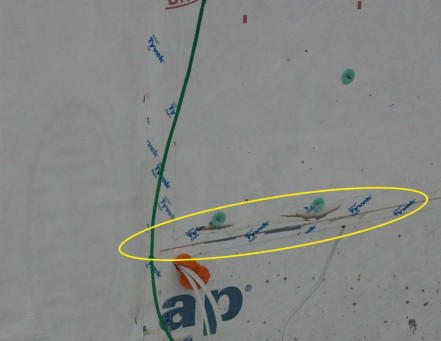
the wrinkle in the wrap. Note that the wrap is wrapped into the door
frame so water can migrate horizontally past the door frame and into
the interior.
In the above photo note the dark line of debris at the horizontal seam
which continues to the vertical seam.
There have been litigation cases where the major contributing factor was improper sealing of the house wrap causing major structural damage to the wood sheathing and other building components. Except under rare circumstances where the reverse lap is part of a small repair, Quality Built would never recommend the reverse lap installation. Manufacturer’s window installation details no longer recommend wrapping the wrap into the opening and then taping the window head nailing flange to the wrap as an effective means of sealing the window. They now indicate a weatherboard installation.
We have contacted one of the larger manufacturers about this and asked about the possibility of a double-sided tape for use on the horizontal seams and were informed that they make such a tape, but it is not for sale in the US. We will be contacting all of the manufacturers to attempt to encourage them to provide a double-sided tape or other method to eliminate the reverse lap. Until then when you are sealing the horizontal seams, make sure to follow all of the manufacturer’s instructions and recommendations, including making sure the wrap is clean and dry and that you are installing the tape within the effective temperature range of the tape as stated by the product manufacturer.
Additionally, make certain fasteners and other objects are not installed in a location that will prevent or compromise the complete seal of the tape. Always use a roller to bond the tape and never rely on smoothing it out with your hand.
Care must be taken and attention to detail is critical when installing the seam tape at transitions to avoid gaps between the tape and the wrap.
For any additional information or details always consult your house wrap system manufacturer’s details and specifications.
About the Author
Jeff Hoch
Architect and Field Consultant
- ICC Certified Residential Inspector
- InterNACHI Certified
- Professional Inspector
- Energy Inspector
- Renovator Inspector
- Lead Inspector
- OSHA 30 Hour certified Scaffold Safety Ladder Safety IAC2 Certified Mold Inspector