Quality Built® Tech Alert
October 15th, 2015
Volume 2, Issue 12
THE ISSUES OF CPVC COMPATABILITY
By: Jeff Hoch
Forensic Architect, Field Consultant and
Technical Services Technician at Quality Built
CPVC piping is used for a variety of purposes in many projects across the country. CPVC stands for chlorinated polyvinyl chloride, which is a thermoplastic material generally used for piping in buildings. CPVC is PVC in which a portion of the hydrogen has been replaced with decomposed chlorine in the form of free radical chlorine. The reason why CPVC is used in plumbing systems as opposed to PVC is the fact that the added chlorine increases the effective temperature range of use for the CPVC piping material. Additionally CPVC is available in CTS (Copper Tube Size) whereas PVC is only available in NPS (Nominal Pipe Size). This CTS sizing makes CPVC easier to use as an alternative to copper piping. CPVC piping can be used for potable water supply and while we see this with some builders in certain regions the largest use is for fire sprinkler installations.
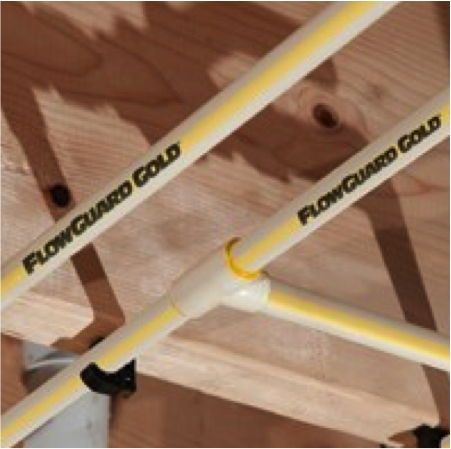
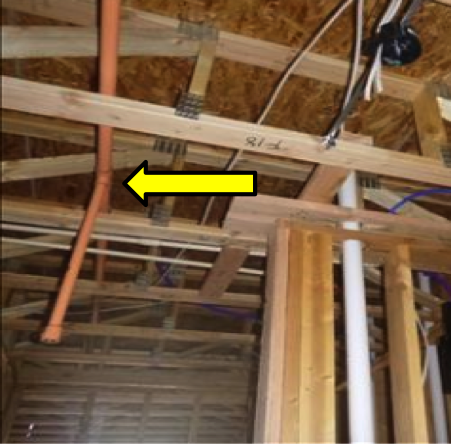
As with many materials used in construction, CPVC has a list of other materials with which it is incompatible. Unlike the incompatibility issue with dissimilar metals, many people are unaware of a similar issue with CPVC. There are many items used in construction and daily life which are incompatible with CPVC. Some of these items will cause problems which make the incompatibility immediately apparent, while others will cause hidden stress cracks that will lie in wait and surprise everyone at some future point. There currently are many large defect litigation cases resulting from leaking CPVC piping related to incompatible products causing environmental stress cracks in the piping.
Some of these incompatible items include hydrocarbons such as non-CPVC compatible cutting oils, termiticides, insecticides, surfactants, cooking oils, plasticizers, building caulks, and certain paints. Additionally, rubber and flexible plastic materials containing certain types of plasticizers pose compatibility issues with CPVC. Incompatible plasticizers include, but are not limited to, phthalates, adipates, trimellitates, and dibenzoates. Materials which may contain incompatible plasticizers include, but are not limited to, caulks, rubber hanger padding, vinyl dip coating on metal parts, rubber gaskets, electrical wire jacketing, electrical tape, and flexible hoses or tubes. Additionally leak testing solutions including dish soap (a surfactant), which is often used for leak testing, can be incompatible.


So did you notice the cooking oils in the list above? This means that CPVC pipe installed in kitchen areas must be protected from contact with grease or cooking oils not only in terms of the items being splashed or spilled on the piping but also from airborne grease or oil that results from cooking. Think of those canned, cooking oil sprays and the fact that the aerosolized spray may be getting on the pipe through gaps around the escutcheon at the sprinkler head. Or have you ever cleaned the screen on your range hood and noticed all of the greasy buildup? How much oil has to get on the pipe before a stress crack develops? How much water pressure will it take to make the pipe burst at this crack? Unfortunately, the answers to these questions are not available at this time. We are not aware of any testing having been performed to determine the maximum amount of cooking oils that can be on the piping before the stress cracking will develop. Also failure pressures may well vary depending on the extent of the stress cracking which may well vary depending on the type of incompatible material and the extent of contact.


On the plasticizer front information points particularly to Cat 5 cabling as causing failures from stress cracking. It is not uncommon to see this wiring lying on top of the piping in attics. As you are preparing contracts, are you spelling out who is responsible for making sure cables, etc. do not come in contact with the CPVC piping? Does this responsibility work with the construction sequencing?
Wiring in contact with CPVC piping in the attic is a common occurrence.
Earlier this year I was having this discussion with a builder and while they had the responsibility on the plumber, the plumbing was being installed before the electrical wiring. The result was that the plumber was done with their rough install before the electrician performed his work and the plumber was not back again until after the drywall was installed. How was the plumber to prevent the contact when they were not on the job to notice and correct the contact?
Fortunately or unfortunately I do not have any failure photos to include with this article however many are available online on websites dedicated to either plastic failures or to the lawsuits resulting from the failures. So I have included photographs showing installations that may result in future failures.
At the 2015 PCBC Homebuilding Trade Show in San Diego, I explained to our walkthrough clients, CPVC pipe as manufactured by the various manufacturers is a good product, when properly installed following the manufacturer’s written instructions and using only products known to be compatible with their product. We recommend that either a third-party inspection be performed just prior to insulation and drywall or that the contracts and Scope of Work spell out who is responsible. Either way the third-party inspector or the sub-contractor responsible will need to work with in the sequence of construction to observe the installation prior to it being covered. At Quality Built, we have customized Checkpoint templates for the various manufacturers. These Checkpoint templates help our inspectors look for high-risk issues including potential material incompatibilities.
ABOUT THE AUTHOR
Jeff Hoch is a Forensic Architect, Field Consultant and Technical Services Technician at Quality Built.
Jeff has been a Licensed Architect for over 18 years. Jeff has worked as a forensic plans examiner and inspector for 18 of the past 25 years, as well as performing construction quality assurance inspections for over 10 years. He has performed thousands of inspections, while providing plans review, forensic inspections, and testing in many states. Jeff has an in-depth knowledge of Building Codes, Design Standards, Local Ordinances, Forensic Building Failure Analysis, and Construction Defects.
You can reach Jeff at: [email protected]
Quality Built's Commitment
Quality Built is committed to being a visionary leader in the insurance, financial and construction industry by providing reliable and innovative Third Party Quality Assurance Services to our clients and by providing those services in the most professional and efficient manner utilizing cutting-edge technology, proprietary software and employees who maintain the highest level of integrity and expertise.
Contact Quality Built today at 800-547-5125 or email: [email protected]